The proceeding is a re-post of an article written by Amanda Pedersen of MD+DI on June 19th, 2020. The original can be found here.
Velentium CEO Dan Purvis is first and foremost a family man. It's apparent on the leadership bio page of his company's website, and it was plenty apparent Thursday afternoon during an interview that takes us behind the scenes of a COVID-19 ventilator initiative known as Project V.
On the evening of March 18, Purvis kissed his wife on the top of her head because she was weeping and couldn't raise her face to kiss him goodbye. Who could blame her, really? Her husband was about to fly to Seattle, WA right around the time coronavirus-related deaths were spiking in that area. But it was a trip he just had to take.
"I turned to my wife — we have four young kids — and I said, 'Babe, you know I have to do this.' It's kind of what all the first responders were having to go through, right? I mean yeah, it may be dangerous, but our country stands in the balance," Purvis said.
That trip ultimately led to Houston, TX-based Velentium playing a key role in ramping up the nation's ventilator stockpile as part of Project V.
Velentium has been building test-stand systems for Bothell, WA-based Ventec Life Systems for five years. Ventec makes a five-in-one machine known as the VOCSN system, which integrates a ventilator, oxygen concentrator, cough assist, suction, and nebulizer into a single system.
Purvis' co-founder at Velentium, Tim Carroll, read a Forbes article published March 14 quoting Ventec CEO Chris Kiple saying that his company could increase its ventilator production five-fold if it had the resources. So Purvis and Carroll called Kiple, and it eventually became apparent that an in-person meeting in Ventec's "situation room" was in order.
"I went through an empty airport and flew on an empty airplane into Seattle, where the first American deaths had been, it's nine miles from the ventilator plant, and it was a crazy time," Purvis told MD+DI.
Purvis and Carroll started Velentium eight years ago with the goal of changing lives for a better world.
"It sounds kind of trite, but it really is the heartbeat of who Tim and I are," Purvis said. "So all a sudden here is this opportunity to literally change lives for a better world. I mean, our devices that we design, develop, and manufacture go into people — as neurostimulators and other devices — and ultimately help them, but here's a chance on a grand scale, a public, global scale, to step in and save lives."
So Purvis met with Ventec executives the morning of March 19 to see if Velentium could help them increase production from 150 ventilators a month to, maybe 300 ventilators a month.
"And they said, 'By the way, there are people from General Motors coming tomorrow'. I was like 'Wait, General Motors? Why is that?' They said, 'We're not really sure, but they're going to be here'," Purvis said.
It turned out that the multi-national automotive maker had a shuttered plant in Kokomo, IN that, once converted, could handle 10,000 ventilators a month for the federal stockpile.
"It was crazy," Purvis said. "Within an hour they had 80 buyers from around the world buying parts for ventilators."
Through Project V, General Motors (GM) is ramping up to produce more than 10,000 Ventec ventilators a month with the ability to scale further if needed. The first 600 ventilators were shipped within weeks of activation, and the company is on track to deliver at least 30,000 ventilators by the end of August to ensure there is inventory on hand for any future demand.
How Has Project V Impacted Velentium?
"At first, we thought we were going to spin up our manufacturing site in Houston to build ventilator components, maybe even build ventilators. And it became very obvious to me that my entire company's capacity was about to be completely overwhelmed with just test systems to test ventilators," Purvis said.
Velentium wasted no time. On Saturday, March 21, the company started sourcing and purchasing parts for the ventilator test systems. It was a scary time, Purvis admitted, because Velentium bought over 1,500 different parts, each in very large quantities, and GM hadn't even made an official purchase order yet.
So why was Purvis — a family man with a wife and four young children — willing to bet his company on this project? Because it was the right thing to do, he said.
"If they wanted to manufacture ventilators in Kokomo, Indiana, for every step, every line worker putting that part together, there's eventually a test step that makes sure that part is right. And because of medical quality, you can't skip the test step. The only thing worse than not having enough ventilators when your mom or my mom is in the ICU is that there's two ventilators but they're both bad and they're going to kill them both," Purvis said. "So they have to be right, and it's my test stands that ensures that those ventilator parts are right."
Within the short span of four weeks:
- Velentium provided the initial 90 test systems out of a total 141 to ensure the respiratory systems met FDA-approved design standards.
- The company shipped the first test system just four days after receiving GM’s original purchase order.
- Velentium scaled its internal team, adding more than 60 contractors in project-based engineering, technical, purchasing, and receiving roles, recruiting talent from industries crippled by the pandemic, including oil and gas.
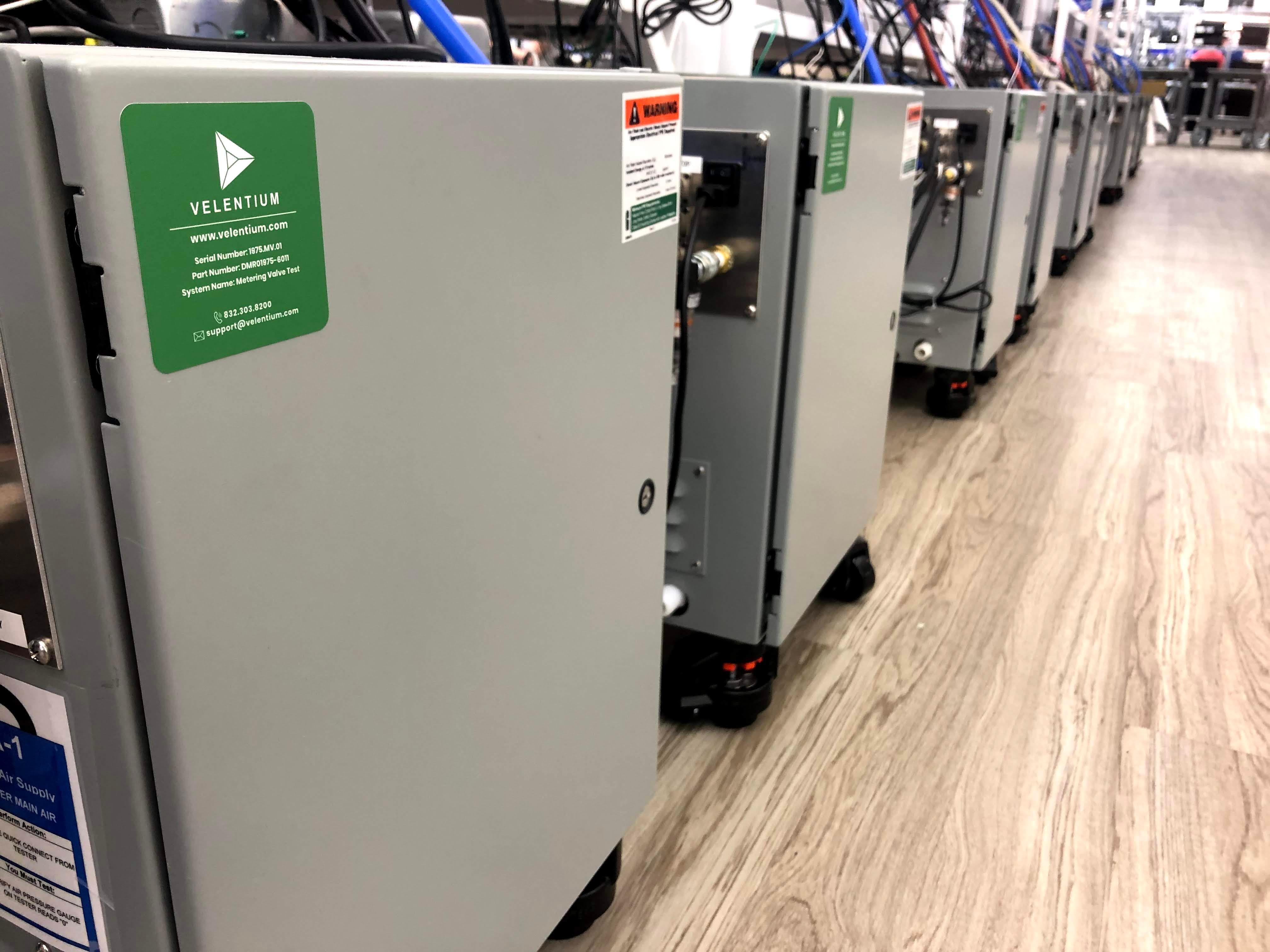
How Did They Pull It Off?
Velentium might not have been able to meet its obligations for Project V had this family man not been willing to risk so much on a purchase order that had not officially come in yet.
"That's how we were able to ship the first test system just four days after receiving the purchase order," Purvis said. "Because we were already building."
Velentium was officially selected to source, assemble, document, verify, and supply the automated test systems to test ventilator parts in GM's newly converted factory.
Then, Purvis and Carroll grew Velentium workforce from 47 to well over 100. That addition included a lot of sub-contractors and contract workers that happened to be based in Houston, Texas where the oil industry was at a stand-still because of COVID-19. So with a deep pool of competent people available to work on a temporary basis, Velentium started interviewing people all day long. If the candidate's first question for Velentium was about money, they probably didn't get the job.
"We weren't afraid to pay people, and we did pay people well," Purvis said. "But I wanted people that were in it for the cause."
When asked if the company split everyone into multiple shifts to work around the clock, Purvis said they didn't have that luxury. Instead, everybody was asked to work one 18-hour shift. The company sent everybody home at 11 p.m. and between 5 a.m. and 6 a.m. they would all show up and do it again, day after day.
"Around Day 9, you started to fall apart, so you'd take a day off, sleep until you were better, and then come back and keep going," Purvis said.
It's something that Purvis says he would never ask anyone in his company to do, under normal circumstances.
"I certainly wouldn't ask it of myself, I've got four young kids," he said. "And yet, this was not a business deal. ... The [COVID-19] curves in mid-March were even steeper than most other countries, including Europe, and were showing no signs of flattening. ... When it really is that dire, at that point you step in and do whatever it takes."
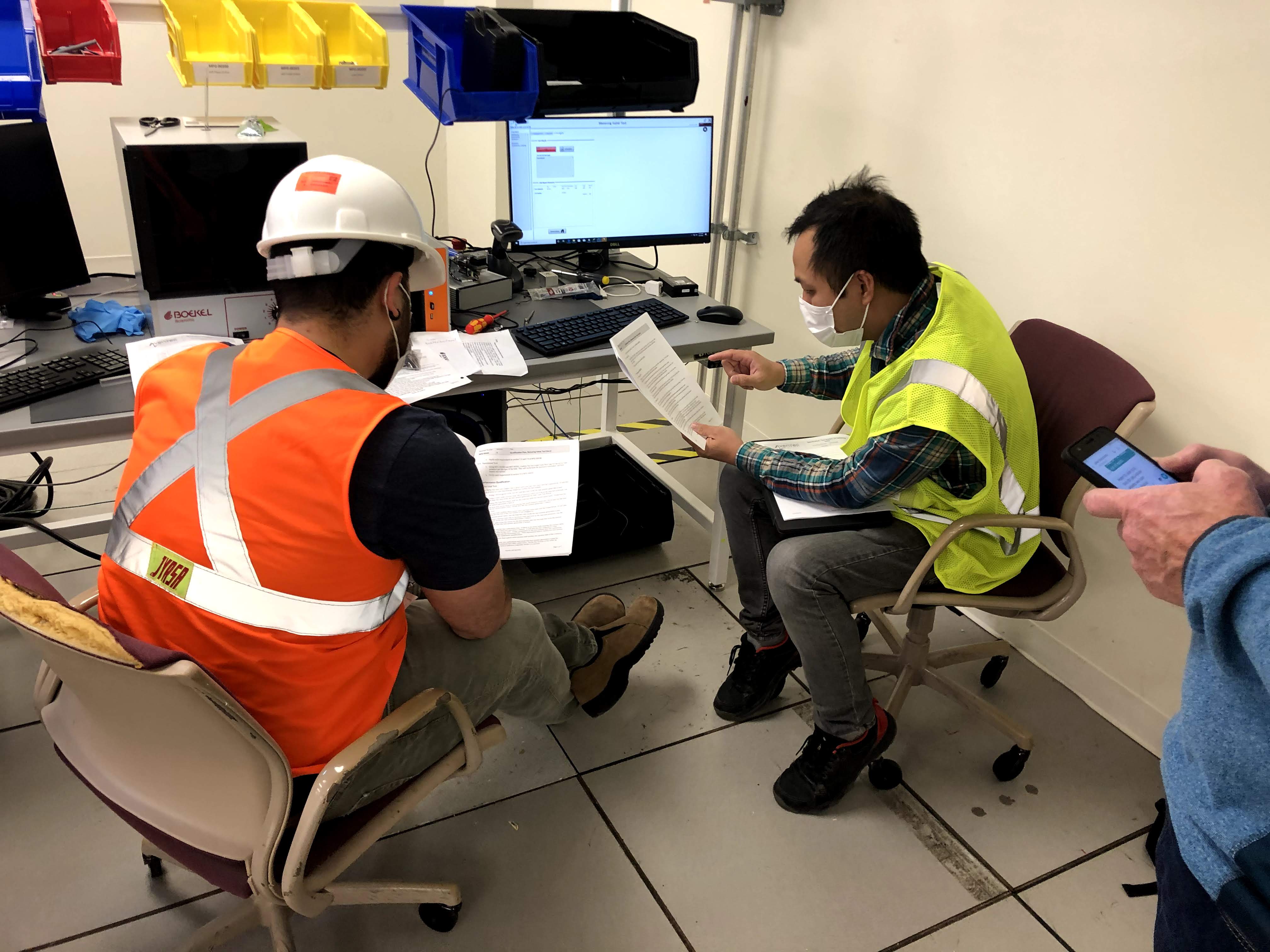
Technical Challenges of Delivering 141 Ventilator Testing Systems During a Pandemic
Velentium had to source parts to build its ventilator testing systems, then deliver the testing systems to GM at breakneck speed. So it's no wonder Purvis had the UPS president of a four-state region (Texas, Oklahoma, Louisiana, and Arkansas) on speed dial.
"They had their first truck every morning loaded with just our stuff, coming to our factory," he said.
So instead of a 10 a.m. or 10:30 a.m. delivery, would get that delivery between 6 a.m. and 7 a.m. And even that wasn't always enough, not because UPS couldn't deliver, but because Velentium's suppliers sometimes needed extra time, Purvis said. When that happened, someone from Velentium would fly to that supplier's city to pick it up. Purvis would tell the supplier to have the part at the hotel's front desk by 6 a.m. That way, his staff person could pick the part up on their way out the door to the airport and be back in Houston by 10 a.m.
Why? Because every hour mattered.
"It could set things back a day, two days, three days if you don't have all the necessary parts," he said.
On the shipping side the question became, how does Velentium get the assembled product from Houston, TX to Kokomo, IN safely for Project V?
"We sent the first test system on a plane with one of our engineers, same day, and that was kind of a nightmare," Purvis said. "Then, General Motors said, 'We've got you.' And they chartered three different jets that just took our test systems directly to Kokomo Municipal Airport, seven miles from the plant."
Suffice is to say, Project V presented a massive technical challenge for Velentium.
"The sheer magnitude of effort to source the parts, receive the parts, build the parts, and then ship the parts was all one thing, to build these test stands," Purvis said. "But then we had 141 test stands arriving in Kokomo, IN and you have to do installation qualification, operation qualification, and then full performance qualification."
GM ended up sending 50 of its engineers to Houston, TX where Velentium medical engineers trained GM automotive engineers on how to do medical validation, and then Velentium supervised while the GM engineers did the validations.
Human Challenges of Delivering 141 Ventilator Testing Systems During a Pandemic
When you've got a workforce that is putting in 18-hour days under that kind of stress, there's bound to be human challenges.
"The founder of Ventec, who is not the CEO anymore, he said, 'you know, a year from now we're all going to be dead, heroes, or in prison'." Purvis laughed. "And I think he's kind of right. Either we can't pull this off and the curve doesn't flatten and like 10% of the population just gets it and dies, or they get it but they don't die because there's ventilators everywhere now and now we're heroes, or we do something really, really wrong and we fall into group think and you look back and say, 'how did we miss that' and ... that could be bad."
And then there was the pressure of dealing with other suppliers who didn't quite get the urgency of the situation.
"I got yelled at by somebody who was like, 'why are you calling me on a weekend?' and I was like, 'well sir, we're trying to save the world'," Purvis said. "I would start hitting executives on LinkedIn for a company I needed to get to until I got one to respond to me. They either got it or they didn't and most of them did get it."
But the human challenge was to keep an upbeat, positive, even temper in the midst of all that pressure.
Purvis held "mid-day" meetings at 5:30 p.m. and he would kick off that meeting everyday by asking his staff to tell him about a human moment. Something that assured both of them that they were still human and not just an output producer.
"It could be that you made breakfast for your daughter and she smiled at you. Or, I screamed at the AMEX lady and I shouldn't have. It was not always a good thing but it does show humanity and emotion and it was those times, the first 15-minute of that call every day, where you kind of go, okay, we're in this together, we have the same goal, we're all trying to do the same thing, so let's give each other the benefit of the doubt."
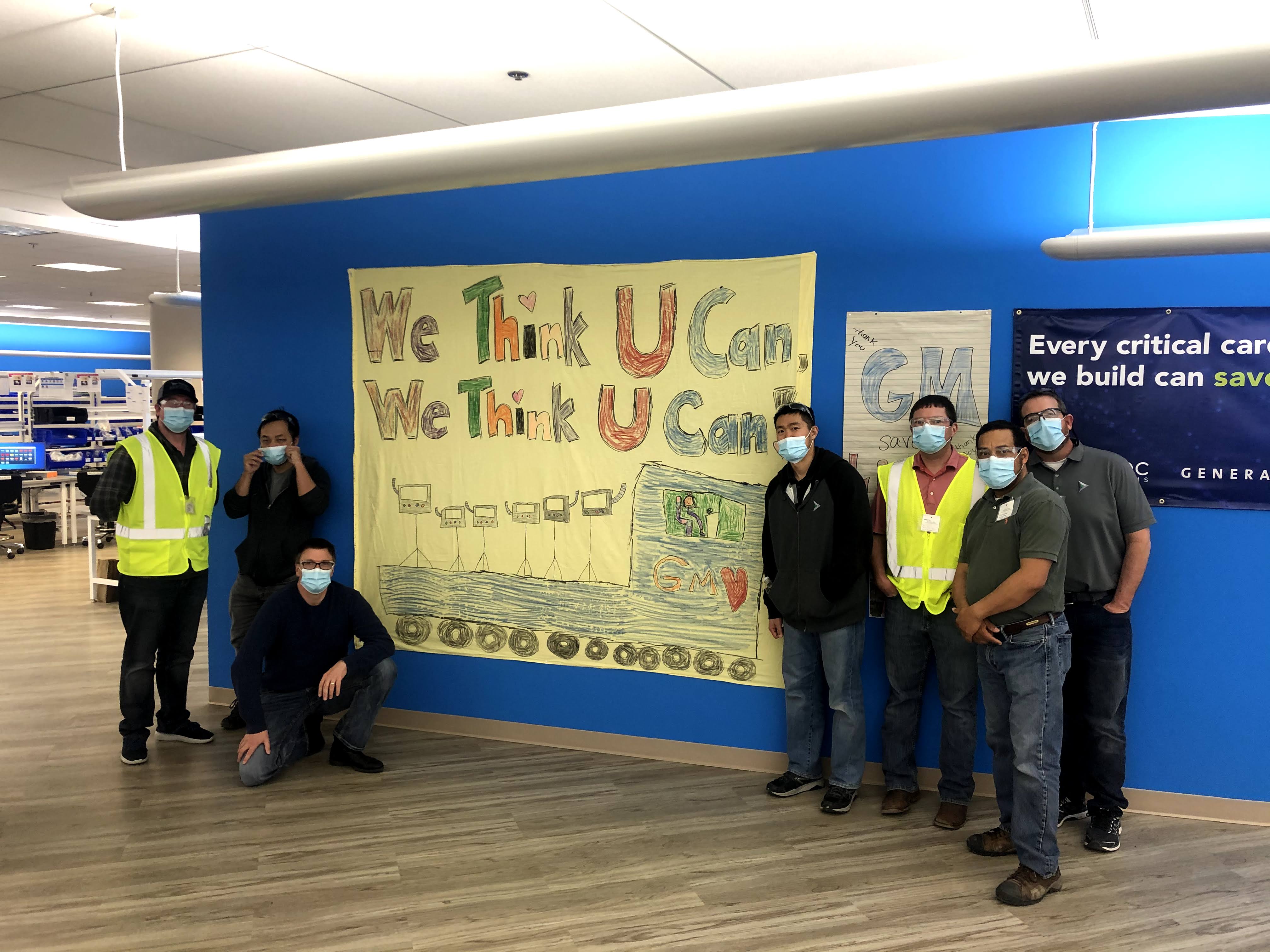
And Project V gave Velentium the chance to prove to the world what it was made of.
"I would sit there and look at the news at the end of the day and see the Vice President talking about our project from the Rose Garden. ... I mean, Mike Pence came to the factory and I got to meet Mary Barra, the CEO of GM," Purvis said. "When we started this company eight years ago around a culture of changing lives for a better world, I believed that we were capable of greatness, and suddenly on this world stage we got to show the world that in fact, yeah, it can work. It was not easy, but man, it was thrilling."
But that validation paled in comparison to the support he received from his family. In fact, soon after that March 18 flight to Seattle, Purvis' wife called him.
"She said, 'you know, the more I watch this news, this disease is really, really scary. Do what you need to do. Do it well, and save our family, and save the country'," he said. "It's been really fun for me to watch our entire staff have that reinforcement from their families. ... I've said for years, we exist to change lives for a better world and that starts with your family."